The Airline 2940
Today on the bench is an Airline model GAA-2940 console produced sometime between 1966-67. Airline was a brand used by the Montgomery Wards department store.
This unit features AM/FM radio, a Voice of Music turntable, and a line level input for tape (which can also be used to input audio from a digital device such as an iPod).
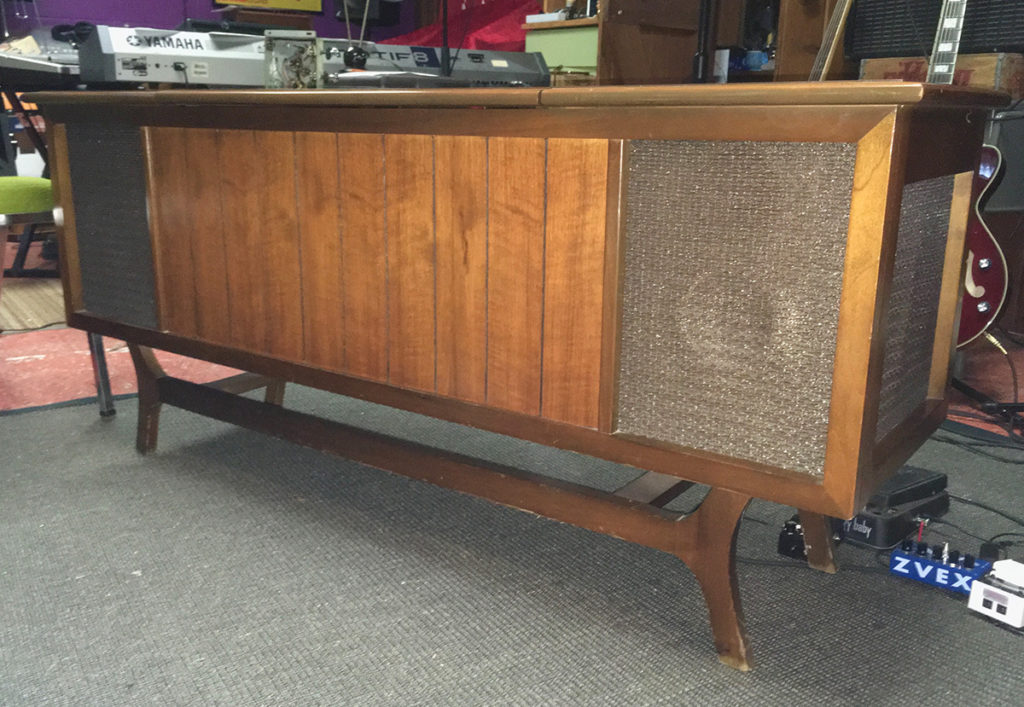
The owner had just bought it to feature in their new home: a midcentury gem that this would feel right at home in. My task was to ensure it had another 50 years of life in it.
After turning it on and listening, it was clear that it needed some TLC. The unit had a slight hum, and the overall sound quality was just a little “off”.
Technical Specifications
The Airline model GAA-2940 console is a solid state amplifier, AM/FM radio, and turntable with the following specs:
- 10 Watts per Channel Audio Power Output at 10% distortion
- 30 – 12kHz frequency response
- Delco DTG 110 Germanium Output transistors
- Class AB configuration
These specs should tell you that this unit is not a real performer in terms of output power or high fidelity audio reproduction. However, its midcentury modern style is not without charm, so we’re going to try and make it sound as good as we can.
The 2940 came with a nice original schematic (with parts list) and a cool owner’s manual.
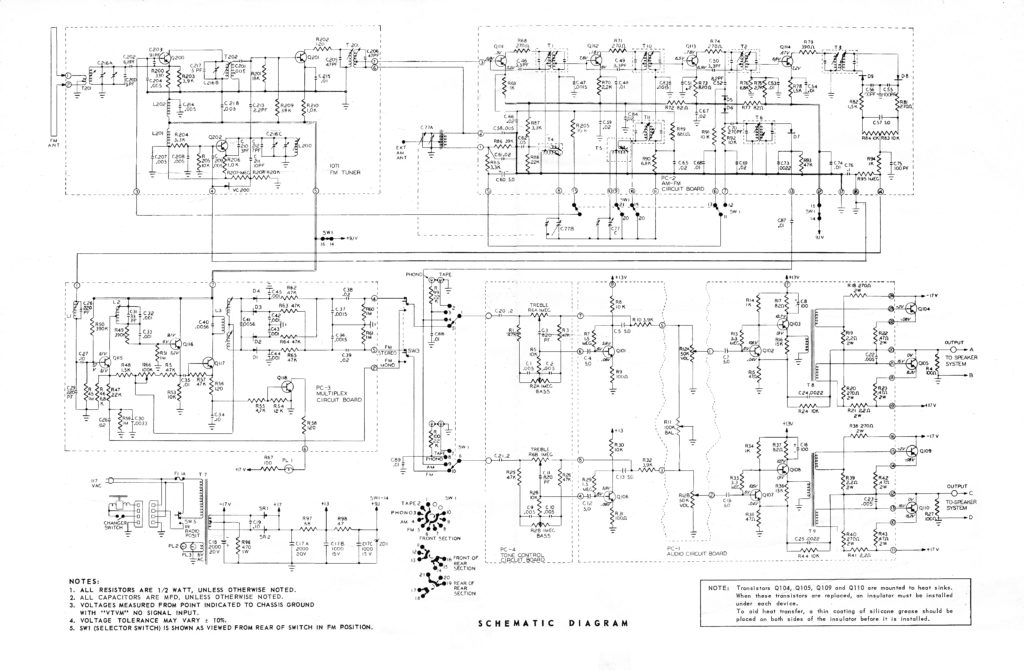
First things First: Rebuilding the Power Supply
The first order of business was to look into the source of the hum, which often indicates an issue in the power supply – often old leaky filter caps. With electrolytic capacitors in a unit this old, I generally replace them with modern high quality capacitors (long life, high temp). So my first task was to rebuild the power supply.
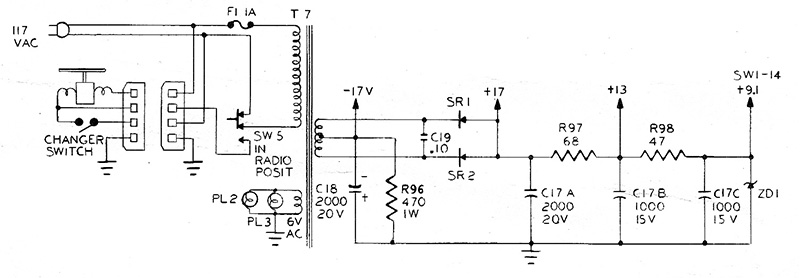
C17A, C17B, and C17C were a multisection can capacitor which was removed. C18 was a very large electrolytic which was also removed. I prefer not to use replacement multisection caps for two reasons: 1) Multisection can caps are expensive and 2) Multisection can caps are generally only rated for 1000-2000 hours at 85 degrees Celsius.
For power supply replacement caps, my preference is for using individual Nichicon UPW series caps mounted on a terminal strip. These are rated for long life (2000-8000 hours) at high temperature (105 degrees). You get a more reliable, rugged cap for a price a fraction of what you might spend on a multisection can cap.
In this power supply circuit I also replaced R96, R97 and R98 with metal film resistors, as the carbon composition resistors in the unit had drifted out of tolerance.
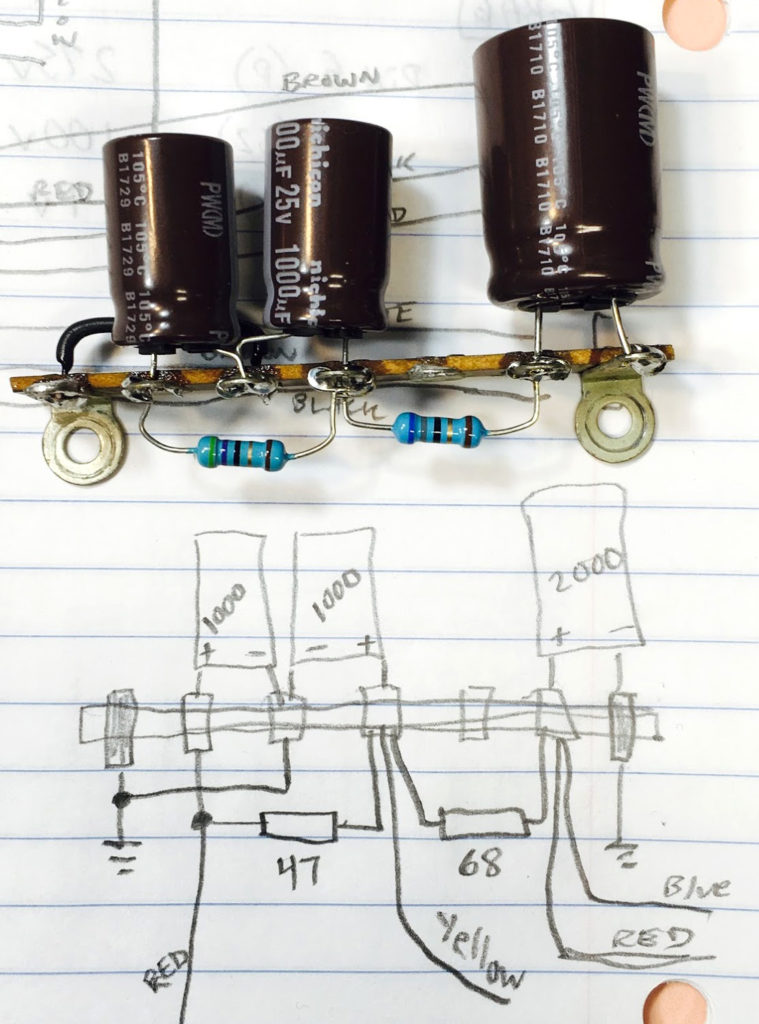
Ciao, Ye Olde Electrolytics
I then replaced the electrolytic capacitors on the preamp/amp board. The old caps had drifted quite a bit and were very leaky.
Cleaning Pots & Switches
I always clean all switches with DeOxit D5 and potentiometers with SuperWash (or other contact cleaner that plays well with carbon such as DeOxit F5).
But… The HUM!
After rebuilding the power supply and replacing the electrolytics, the sound was much improved – however, with the volume at 0, a mysterious hum persisted that drove me to look deeper into the cause.
Using an oscilloscope, I was able to visualize the hum and it appeared to be a combination of 60 and 120 cycle frequencies.
In order to ensure this hum was not coming from the power supply circuit at all, I replaced the rectifier diodes, which looked a little scorched, with 1N4004 diodes.
I also implemented best practices for grounding components after finding that there were many points on the chassis that different components were grounded to – including the 6.3VAC lamp circuit. I unsoldered the pots from the chassis and connected them to a star ground, along with the preamp board.
After many hours of work, the hum was only reduced slightly. None of these things eliminated the hum entirely. Using an injected sine wave and oscilloscope, I was able to isolate where the hum was coming from – the output stage.
Learn how I solved the hum problem in Part 2 of my repair saga.